The performance of 18-gauge brad nails in terms of energy efficiency compared to traditional fasteners depends on the specific application and the tools used for installation. Brad nails are generally smaller in diameter and have a smaller head than traditional fasteners, such as larger gauge nails or screws.
Here are some considerations regarding the energy efficiency of 18-gauge brad nails:
- Smaller Hole Size:
- One advantage of using 18-gauge brad nails is that they create smaller holes compared to traditional fasteners. The reduced hole size can lead to less material displacement, potentially minimizing the amount of energy required for installation.
- Less Material Disruption:
- Brad nails are designed to have minimal impact on the surrounding material. This can be advantageous in terms of energy efficiency, especially when working with delicate or thin materials where larger fasteners might cause more disruption.
- Reduced Surface Damage:
- The smaller diameter and head of 18-gauge brad nails may result in reduced surface damage to the material being fastened. This can be important in applications where maintaining the appearance of the material is crucial.
- Lower Penetration Resistance:
- Smaller gauge brad nails may encounter less resistance when driven into the material, potentially requiring less energy for installation compared to larger, higher-gauge fasteners that need more force to penetrate.
- Lower Fastening Strength:
- While 18-gauge brad nails are suitable for many applications, they may not provide the same level of holding power as larger fasteners. In situations where high holding strength is critical, traditional fasteners might be more appropriate.
- Use with Pneumatic Tools:
- Energy efficiency can also be influenced by the tools used for installation. Brad nails are often installed using pneumatic nail guns, which can be more energy-efficient compared to traditional screwdrivers or manual nailers.
- Precision Fastening:
- Brad nails are well-suited for precision fastening tasks where accuracy is crucial. Their smaller size and reduced impact can contribute to more precise installations, potentially reducing the need for rework.
It’s important to note that the choice between 18-gauge brad nails and traditional fasteners depends on the specific requirements of the project. In situations where high holding power and structural integrity are paramount, traditional fasteners may be more suitable. However, for applications where minimizing surface damage, achieving a clean finish, and precision fastening are priorities, 18-gauge brad nails can offer advantages in terms of energy efficiency and effectiveness. Additionally, advancements in tool technology, such as improved pneumatic nail guns, contribute to overall energy efficiency in fastening applications.
What measures are taken to prevent degradation of 18 gauge brad nail in high-temperature environments?
18-gauge brad nails are commonly made of steel, and like many metals, they can be susceptible to degradation in high-temperature environments. Elevated temperatures can lead to various issues such as loss of strength, increased susceptibility to corrosion, and changes in the material properties.
To prevent degradation of 18-gauge brad nails in high-temperature environments, manufacturers and users can take several measures:
- Material Selection:
- Choose a material for the 18-gauge brad nails that is specifically designed to withstand high temperatures. This may involve selecting heat-resistant steel alloys that maintain their structural integrity at elevated temperatures.
- Heat Treatment:
- Apply heat treatment processes during the manufacturing of the brad nails. Heat treatment can enhance the material’s strength, hardness, 18 gauge brad nail and resistance to high temperatures. Specific heat treatment methods, such as quenching and tempering, can be employed based on the material used.
- Coating for Heat Resistance:
- Apply coatings that provide heat resistance to the brad nails. Some coatings are designed to protect the metal from the effects of high temperatures, preventing oxidation and maintaining the material’s properties.
- Thermal Barrier Coatings:
- Consider using thermal barrier coatings that act as insulating layers, protecting the brad nails from direct exposure to high temperatures. These coatings can help maintain the temperature of the fasteners within acceptable limits.
- Application Considerations:
- Avoid using 18-gauge brad nails in applications where they will be consistently exposed to extreme temperatures. Understanding the intended application and environmental conditions is crucial for selecting the appropriate fastener.
- Ventilation and Cooling:
- Ensure proper ventilation and cooling in the environment where the brad nails are used. Adequate airflow can help dissipate heat and prevent the fasteners from reaching temperatures that could lead to degradation.
- Installation Guidelines:
- Follow manufacturer guidelines for the installation of brad nails, including recommendations for temperature limits. Improper installation, such as excessive friction during driving, can generate additional heat that may affect the fastener’s performance.
- Monitoring and Inspection:
- Regularly monitor and inspect the brad nails for signs of degradation, including changes in color, corrosion, or loss of structural integrity. Early detection of issues allows for timely replacement and maintenance.
- Consider Alternative Materials:
- In applications with extremely high temperatures, consider alternative fastener materials that are specifically designed for use in such environments. Heat-resistant alloys or materials with higher temperature tolerance may be more suitable.
It’s important to note that while these measures can help mitigate the impact of high temperatures on 18-gauge brad nails, there may still be limitations based on the specific material composition and the severity of the environmental conditions. Always refer to the manufacturer’s recommendations and guidelines for the proper use of fasteners in different temperature environments.
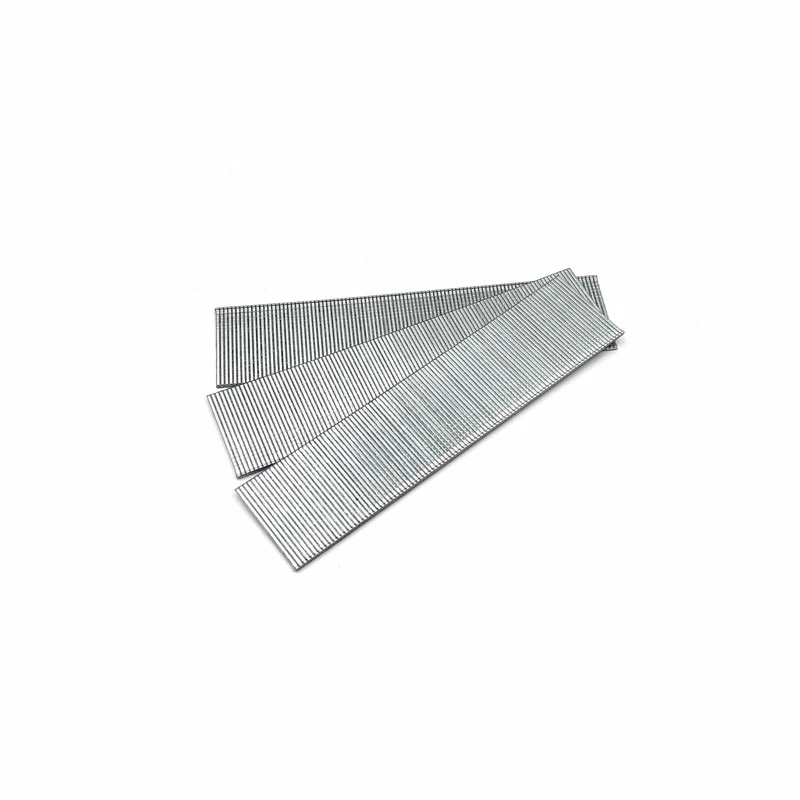